A liquid rocket engine (LRE) is a rocket engine that uses liquid propellants. Liquid propellants are stored in tanks and fed into the engine's combustion chamber, where they are burned to produce hot gases. These gases are then expelled through the engine's nozzle, providing thrust. LREs are used in a variety of applications, including spacecraft propulsion, launch vehicles, and missiles.
LREs offer several advantages over other types of rocket engines. First, they are relatively efficient, converting a high percentage of the propellant's energy into thrust. Second, they are throttleable, meaning that their thrust can be adjusted to meet the needs of the mission. Third, LREs can be restarted multiple times, making them suitable for missions that require multiple burns. Finally, LREs can use a wide variety of propellants, including liquid hydrogen, liquid oxygen, kerosene, and methane.
The first LRE was developed in the early 1900s by Robert Goddard. Goddard's engine used liquid oxygen and gasoline as propellants. In the years since, LREs have been used to power a wide variety of spacecraft, including the Saturn V rocket that took humans to the moon. Today, LREs are the most common type of rocket engine used in space applications.
Liquid Rocket Engine
Liquid rocket engines (LREs) are a type of rocket engine that use liquid propellants. They are widely used in spacecraft propulsion, launch vehicles, and missiles. LREs offer several advantages over other types of rocket engines, including high efficiency, throttleability, and the ability to be restarted multiple times.
- Propellants: LREs use a variety of propellants, including liquid hydrogen, liquid oxygen, kerosene, and methane.
- Combustion: Propellants are burned in the engine's combustion chamber to produce hot gases.
- Nozzle: Hot gases are expelled through the engine's nozzle to provide thrust.
- Efficiency: LREs are relatively efficient, converting a high percentage of the propellant's energy into thrust.
- Throttleability: LREs can be throttled, meaning that their thrust can be adjusted to meet the needs of the mission.
- Restartability: LREs can be restarted multiple times, making them suitable for missions that require multiple burns.
- Reliability: LREs are generally very reliable, with a long history of successful use in space applications.
- Applications: LREs are used in a variety of applications, including spacecraft propulsion, launch vehicles, and missiles.
- History: The first LRE was developed in the early 1900s by Robert Goddard.
LREs have played a vital role in the development of space exploration. They were used to power the Saturn V rocket that took humans to the moon, and they are currently used to power the Space Shuttle and a variety of other spacecraft. LREs are also being developed for use in future missions to Mars and other planets.
Propellants
Propellants are the fuels and oxidizers that are burned in a liquid rocket engine (LRE) to produce thrust. The choice of propellants has a significant impact on the performance of the engine, including its efficiency, specific impulse, and thrust-to-weight ratio.
- Liquid hydrogen (LH2) is a high-performance propellant that is often used in upper-stage engines. It has a high specific impulse, but it is also very cold and difficult to handle.
- Liquid oxygen (LOX) is a common oxidizer that is used in many LREs. It is relatively inexpensive and easy to handle, but it has a lower specific impulse than LH2.
- Kerosene is a hydrocarbon fuel that is often used in first-stage engines. It has a lower specific impulse than LH2 or LOX, but it is relatively inexpensive and easy to handle.
- Methane is a hydrocarbon fuel that is becoming increasingly popular for use in LREs. It has a higher specific impulse than kerosene, and it is also relatively inexpensive and easy to handle.
The choice of propellants for a particular LRE depends on a number of factors, including the engine's performance requirements, the cost of the propellants, and the availability of the propellants. In general, LH2/LOX engines offer the highest performance, but they are also the most expensive and difficult to handle. Kerosene/LOX engines are less expensive and easier to handle, but they have a lower performance. Methane/LOX engines offer a compromise between performance and cost, and they are becoming increasingly popular for use in LREs.
Combustion
Combustion is the process of burning propellants to produce hot gases. In a liquid rocket engine (LRE), the propellants are typically liquid fuels and oxidizers. The combustion process takes place in the engine's combustion chamber, which is a high-pressure environment. The hot gases produced by combustion are then expelled through the engine's nozzle to produce thrust.
- Propellant Mixing: In order for combustion to occur, the propellants must be mixed together in the combustion chamber. This is typically done using a variety of methods, such as spray nozzles or impinging jets. The mixing process must be carefully controlled in order to ensure that the propellants are mixed evenly and that there is no unburned propellant left in the combustion chamber.
- Flame Stabilization: Once the propellants are mixed, they must be ignited and stabilized in order to sustain combustion. This is typically done using a variety of methods, such as spark plugs or pilot flames. The flame stabilization process must be carefully controlled in order to ensure that the flame does not extinguish or become unstable.
- Heat Transfer: The combustion process produces a great deal of heat, which must be transferred to the engine's nozzle in order to produce thrust. This is typically done using a variety of methods, such as regenerative cooling or film cooling. The heat transfer process must be carefully controlled in order to ensure that the engine's nozzle does not overheat and fail.
Combustion is a critical process in the operation of a liquid rocket engine. The careful control of the combustion process is essential for ensuring that the engine operates efficiently and reliably.
Nozzle
The nozzle is a critical component of a liquid rocket engine (LRE). It is responsible for converting the hot gases produced by combustion into thrust. The nozzle does this by expanding the gases and accelerating them to a high velocity. The faster the gases are expelled, the greater the thrust produced by the engine.
The shape of the nozzle is carefully designed to maximize the efficiency of the expansion process. The ideal nozzle shape depends on the operating conditions of the engine, such as the pressure and temperature of the gases. In general, a longer nozzle will produce more thrust than a shorter nozzle, but it will also be heavier and more complex to manufacture.
Nozzles are typically made of high-temperature materials, such as carbon fiber or ceramic. These materials can withstand the extreme heat and pressure of the exhaust gases. Nozzles are also often cooled by circulating a coolant through the nozzle walls. This helps to protect the nozzle from damage and extends its lifespan.
The nozzle is a critical component of a LRE. It plays a vital role in converting the hot gases produced by combustion into thrust. The careful design and manufacture of the nozzle is essential for ensuring the efficient and reliable operation of the engine.
Here are some examples of the practical significance of understanding the connection between the nozzle and thrust in a LRE:
- Engineers can design nozzles that are optimized for specific applications. For example, a nozzle designed for a rocket that will be used to launch a satellite into orbit will be different from a nozzle designed for a rocket that will be used to land a rover on Mars.
- Understanding the connection between the nozzle and thrust can help engineers to troubleshoot problems with LREs. For example, if a rocket is not producing enough thrust, the engineers can check the nozzle to see if it is damaged or if it is not properly shaped.
- Understanding the connection between the nozzle and thrust can help engineers to design new and improved LREs. For example, engineers are currently working on developing nozzles that are made of new materials that are lighter and more durable than traditional materials.
Overall, the nozzle is a critical component of a LRE. Understanding the connection between the nozzle and thrust is essential for ensuring the efficient and reliable operation of the engine.
Efficiency
The efficiency of a liquid rocket engine (LRE) is a measure of how much of the propellant's energy is converted into thrust. LREs are relatively efficient, converting a high percentage of the propellant's energy into thrust. This is due to the fact that LREs use a closed cycle, which means that the propellants are recirculated through the engine multiple times. This allows the engine to extract more energy from the propellants.
The efficiency of an LRE is important because it affects the amount of propellant that is required for a given mission. A more efficient engine will require less propellant, which can save money and weight. For example, the Space Shuttle main engines are very efficient, and they can convert over 90% of the propellant's energy into thrust. This allows the Space Shuttle to carry more payload into orbit.
Understanding the efficiency of LREs is also important for designing and operating rocket engines. Engineers need to be able to predict how much thrust an engine will produce for a given amount of propellant. This information is used to design the engine and to plan missions.
The efficiency of LREs is a critical factor in the design and operation of rocket engines. By understanding the efficiency of LREs, engineers can design and operate engines that are more efficient and that require less propellant.
Throttleability
Throttleability is a critical feature of liquid rocket engines (LREs) that allows for precise control over the amount of thrust produced. This capability is essential for a variety of reasons, including:
- Precision Maneuvers: Throttleability allows spacecraft to perform precision maneuvers, such as docking with other spacecraft or landing on planetary surfaces. By adjusting the thrust, the spacecraft can be moved with great accuracy and control.
- Efficient Ascent: During the ascent phase of a rocket launch, throttleability can be used to optimize the vehicle's trajectory and reduce fuel consumption. By throttling back the engine, the rocket can climb more efficiently and conserve propellant.
- Safe Landing: When landing a spacecraft on a planetary surface, throttleability is essential for controlling the vehicle's descent and ensuring a safe landing. By gradually reducing the thrust, the spacecraft can be brought to a gentle and controlled landing.
Throttleability is achieved through a variety of methods, including varying the propellant flow rate, adjusting the injector pattern, or using movable nozzles. The specific method used depends on the design of the engine and the desired performance characteristics.
The ability to throttle LREs provides significant advantages for spacecraft missions. It allows for greater precision and control during maneuvers, more efficient ascent and descent trajectories, and safer landings. As a result, throttleability is a key feature of many LREs used in space exploration and other applications.
Restartability
The restartability of liquid rocket engines (LREs) is a critical feature that enables them to perform missions that require multiple burns. Unlike solid rocket motors, which can only be used once, LREs can be shut down and restarted multiple times, making them ideal for missions such as orbital insertion, rendezvous and docking, and precision landings.
The ability to restart an LRE is achieved through a combination of design features and operational procedures. LREs typically use propellants that are stored in separate tanks and fed into the engine's combustion chamber when needed. This allows the engine to be shut down and restarted without the need to replenish the propellants.
Restartability is particularly important for missions that require multiple burns. For example, a spacecraft that is inserting itself into orbit around a planet may need to perform a series of burns to slow down and achieve the desired orbit. Similarly, a spacecraft that is rendezvousing with another spacecraft may need to perform multiple burns to adjust its trajectory and match the velocity of the target spacecraft.
The restartability of LREs has been a key factor in the success of many space missions. For example, the Space Shuttle's main engines were restarted multiple times during each mission to achieve orbit, rendezvous with the International Space Station, and return to Earth. Similarly, the Apollo lunar module's descent engine was restarted multiple times during the moon landing to achieve a soft landing on the lunar surface.
Understanding the connection between restartability and LREs is essential for designing and operating spacecraft. Engineers must carefully consider the number and duration of burns required for a given mission and select an LRE that meets those requirements. Additionally, operational procedures must be developed to ensure that the LRE is restarted safely and reliably.
Reliability
The reliability of liquid rocket engines (LREs) is a critical factor in their widespread use in space applications. LREs have a long history of successful use in a variety of missions, including satellite launches, space probes, and human spaceflight. This reliability is due to a number of factors, including:
- Robust Design: LREs are designed with robust components and systems that are able to withstand the harsh conditions of space. This includes exposure to extreme temperatures, vibration, and radiation.
- Redundancy: LREs often incorporate redundant systems to ensure that a failure in one system does not result in a catastrophic failure of the engine. For example, many LREs have multiple fuel pumps and injectors.
- Extensive Testing: LREs undergo extensive testing before they are used in space applications. This testing includes ground testing, altitude testing, and flight testing. This testing helps to identify and correct any potential problems before the engine is used in a mission.
The reliability of LREs has been a major factor in the success of many space missions. For example, the Space Shuttle's main engines were used on over 130 missions without a single failure. Similarly, the Apollo lunar module's descent engine was used on six successful moon landings.
The reliability of LREs is essential for the future of space exploration. As we send humans and spacecraft to more distant and challenging destinations, we will need to rely on LREs to provide safe and reliable transportation.
Applications
Liquid rocket engines (LREs) are a versatile and powerful type of rocket engine that are used in a wide range of applications, including spacecraft propulsion, launch vehicles, and missiles. LREs offer several advantages over other types of rocket engines, including high efficiency, throttleability, and the ability to be restarted multiple times.
- Spacecraft Propulsion: LREs are commonly used to propel spacecraft in orbit around Earth and to send spacecraft to other planets. LREs are well-suited for spacecraft propulsion because they are efficient and can be throttled to provide the necessary thrust for different phases of a mission.
- Launch Vehicles: LREs are also used in launch vehicles to launch payloads into orbit. Launch vehicles typically use a combination of solid and liquid rocket engines. LREs are used in the upper stages of launch vehicles because they are more efficient and can be throttled to provide the necessary thrust for orbital insertion.
- Missiles: LREs are also used in missiles. Missiles use LREs to provide the necessary thrust for propulsion. LREs are well-suited for missiles because they are powerful and can be throttled to provide the necessary thrust for different phases of a mission.
The versatility and power of LREs make them an essential part of many space exploration and defense systems. LREs are likely to continue to be used in a wide range of applications for many years to come.
History
The development of the liquid rocket engine (LRE) by Robert Goddard in the early 1900s was a pivotal moment in the history of rocketry. Goddard's LRE was the first to successfully use liquid propellants, which gave it a number of advantages over solid-propellant rockets. Liquid propellants are more efficient, can be throttled, and can be restarted multiple times. This made LREs ideal for a wide range of applications, including spacecraft propulsion, launch vehicles, and missiles.
Goddard's early work on LREs laid the foundation for the development of the powerful rocket engines that were used to launch the first satellites and humans into space. Today, LREs are the most common type of rocket engine used in space applications. They are also used in a variety of military applications, including missiles and launch vehicles.
Understanding the connection between Goddard's early work on LREs and the development of modern rocket engines is essential for appreciating the history of rocketry and the importance of LREs in space exploration and other applications.
Frequently Asked Questions about Liquid Rocket Engines
Liquid rocket engines (LREs) are a type of rocket engine that uses liquid propellants. They are widely used in spacecraft propulsion, launch vehicles, and missiles. LREs offer several advantages over other types of rocket engines, including high efficiency, throttleability, and the ability to be restarted multiple times.
Question 1: What are the advantages of LREs over other types of rocket engines?
Answer: LREs offer several advantages over other types of rocket engines, including high efficiency, throttleability, and the ability to be restarted multiple times.
Question 2: What are the different types of propellants used in LREs?
Answer: LREs can use a variety of propellants, including liquid hydrogen, liquid oxygen, kerosene, and methane.
Question 3: How do LREs work?
Answer: LREs work by burning propellants in a combustion chamber to produce hot gases. These gases are then expelled through the engine's nozzle to produce thrust.
Question 4: What are the applications of LREs?
Answer: LREs are used in a variety of applications, including spacecraft propulsion, launch vehicles, and missiles.
Question 5: Who developed the first LRE?
Answer: The first LRE was developed by Robert Goddard in the early 1900s.
Question 6: What is the future of LREs?
Answer: LREs are likely to continue to be used in a wide range of applications for many years to come.
Summary: LREs are a versatile and powerful type of rocket engine that offer several advantages over other types of rocket engines. They are used in a wide range of applications, including spacecraft propulsion, launch vehicles, and missiles.
Transition to the next article section: LREs are a critical technology for space exploration and other applications. As we continue to explore the solar system and beyond, LREs will play an increasingly important role in our ability to reach new destinations.
Tips for Liquid Rocket Engine Design and Operation
Liquid rocket engines (LREs) are complex and powerful machines that require careful design and operation to perform safely and efficiently. Here are a few tips to help you get started:
Tip 1: Choose the right propellants.
The choice of propellants has a significant impact on the performance of an LRE. Some propellants are more efficient than others, and some are more stable. It is important to choose propellants that are compatible with the engine's design and that meet the mission requirements.
Tip 2: Design the combustion chamber carefully.
The combustion chamber is where the propellants are burned to produce hot gases. The shape and size of the combustion chamber must be carefully designed to ensure that the propellants are burned efficiently and that the heat is transferred to the nozzle properly.
Tip 3: Use a high-quality nozzle.
The nozzle is responsible for converting the hot gases produced by combustion into thrust. The shape and size of the nozzle must be carefully designed to maximize the efficiency of the expansion process.
Tip 4: Test the engine thoroughly.
Before an LRE can be used in a mission, it must be thoroughly tested to ensure that it is safe and reliable. Testing should include both ground testing and flight testing.
Tip 5: Operate the engine carefully.
LREs are powerful machines that must be operated carefully to avoid damage. It is important to follow the manufacturer's instructions for operating the engine and to monitor the engine's performance closely during operation.
Summary: By following these tips, you can help to ensure that your LRE design is safe, efficient, and reliable.
Transition to the article's conclusion: LREs are a critical technology for space exploration and other applications. As we continue to explore the solar system and beyond, LREs will play an increasingly important role in our ability to reach new destinations.
Conclusion
Liquid rocket engines (LREs) are a critical technology for space exploration and other applications. They are powerful, efficient, and versatile, and they have played a major role in our ability to reach new destinations in space.
As we continue to explore the solar system and beyond, LREs will play an increasingly important role in our ability to reach new destinations. They are the key to unlocking the vast potential of space, and they will help us to achieve our dreams of becoming a spacefaring civilization.
Youtube Video:
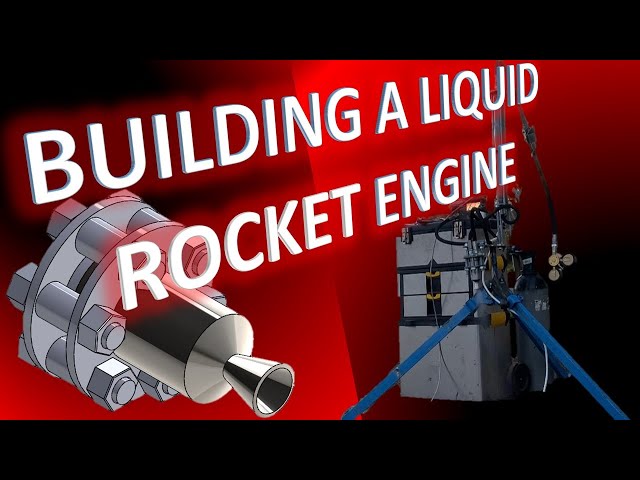