Protofab engineering is a specialized field of manufacturing that utilizes advanced technologies to create prototypes and small-batch production runs. By leveraging techniques such as 3D printing, CNC machining, and injection molding, protofab engineers can rapidly produce functional and cost-effective prototypes, enabling businesses to bring their products to market faster and more efficiently.
Protofab engineering plays a crucial role in product development, allowing designers and engineers to test and refine their concepts before investing in mass production. This iterative approach reduces the risk of costly mistakes and ensures that products meet the desired specifications. Protofab engineering also offers advantages in terms of flexibility and customization, empowering businesses to create tailored solutions that cater to specific market needs.
The field of protofab engineering continues to evolve, driven by advancements in technology and the growing demand for rapid prototyping services. As technology becomes more sophisticated and accessible, protofab engineers will continue to push the boundaries of what is possible, empowering businesses to innovate and bring groundbreaking products to market.
Protofab Engineering
Protofab engineering encompasses a wide range of technologies and processes, each playing a vital role in enabling rapid prototyping and small batch production. Key aspects of protofab engineering include:
- 3D Printing
- CNC Machining
- Injection Molding
- Rapid Prototyping
- Product Development
- Design Iteration
- Cost-Effectiveness
- Flexibility
- Customization
These aspects are interconnected and contribute to the overall value proposition of protofab engineering. For instance, 3D printing enables the rapid creation of complex prototypes, which can then be refined through design iteration, resulting in cost-effective and customized products. The flexibility of protofab engineering allows businesses to adapt to changing market demands and explore novel design concepts.
Protofab engineering is not just a collection of technologies but a mindset that embraces innovation and efficiency. By leveraging the latest advancements in manufacturing, protofab engineers empower businesses to bring their products to market faster, better, and more cost-effectively.
3D Printing
3D printing is a transformative technology that has revolutionized the field of protofab engineering. It enables the rapid creation of physical prototypes directly from digital designs, empowering engineers and designers to iterate and refine their concepts quickly and efficiently. Unlike traditional manufacturing methods, which can be time-consuming and expensive, 3D printing allows for the production of complex prototypes in a matter of hours or days, significantly reducing lead times and development costs.
The integration of 3D printing into protofab engineering workflows has brought numerous benefits. Firstly, it enhances design flexibility, allowing engineers to explore complex geometries and intricate designs that would be difficult or impossible to produce using traditional methods. Secondly, 3D printing enables rapid prototyping, accelerating the product development cycle and allowing businesses to bring their products to market faster. Thirdly, 3D printing reduces production costs, particularly for small batch production runs or customized products.
Practical applications of 3D printing in protofab engineering are diverse. For instance, 3D printed prototypes can be used for functional testing, form and fit analysis, and design validation. This enables engineers to identify and address potential issues early in the development process, reducing the risk of costly mistakes during mass production. Additionally, 3D printing is increasingly used to create custom jigs, fixtures, and tooling, streamlining production processes and improving overall efficiency.
In conclusion, 3D printing is a cornerstone of protofab engineering, enabling rapid prototyping, design iteration, and cost-effective production. Its integration into protofab engineering workflows has transformed the way products are developed and manufactured, empowering businesses to innovate and bring groundbreaking products to market.
CNC Machining
CNC machining, short for computer numerical control machining, is a subtractive manufacturing process that utilizes computer-controlled machines to remove material from a workpiece, resulting in the creation of precise and complex parts. In the context of protofab engineering, CNC machining plays a vital role in the production of prototypes and small batch production runs.
- Precision and Accuracy: CNC machining excels in producing parts with high levels of precision and accuracy, making it ideal for applications where dimensional accuracy is critical. This capability aligns with the demand for precision in protofab engineering, where prototypes must accurately represent the final product design.
- Complex Geometries: CNC machining enables the creation of complex geometries and intricate features that would be difficult or impossible to achieve using manual machining methods. This capability empowers protofab engineers to explore innovative designs and push the boundaries of what is possible.
- Material Versatility: CNC machining can be performed on a wide range of materials, including metals, plastics, and composites. This versatility allows protofab engineers to select the most appropriate material for each application, considering factors such as strength, weight, and cost.
- Rapid Prototyping: CNC machining facilitates rapid prototyping by enabling the quick production of physical prototypes from digital designs. This capability accelerates the product development cycle, allowing businesses to bring their products to market faster.
In summary, CNC machining is an essential component of protofab engineering, enabling the production of precise, complex, and high-quality prototypes and small batch production runs. Its integration into protofab engineering workflows empowers businesses to innovate, reduce lead times, and bring groundbreaking products to market.
Injection Molding
Injection molding is a high-volume manufacturing process that involves injecting molten material into a mold cavity to create precise and complex plastic parts. When combined with protofab engineering, injection molding becomes a powerful tool for producing high-quality prototypes and small batch production runs.
The integration of injection molding into protofab engineering workflows offers several key advantages:
- Rapid Prototyping: Injection molding enables the rapid production of plastic prototypes, expediting the product development cycle and allowing businesses to bring their products to market faster.
- Mass Production Feasibility: Injection molding is a scalable process that can be easily transitioned to mass production, making it an ideal choice for products that require high-volume manufacturing.
- Design Flexibility: Injection molding allows for the creation of complex geometries and intricate features, providing protofab engineers with the design freedom to explore innovative concepts.
- Cost-Effectiveness: For high-volume production runs, injection molding offers significant cost savings compared to other manufacturing methods.
One practical example of the connection between injection molding and protofab engineering can be seen in the development of medical devices. Protofab engineers utilize injection molding to create prototypes and small batch production runs of medical device components, ensuring that the parts meet the stringent quality and precision requirements of the healthcare industry.
In summary, injection molding is an essential component of protofab engineering, enabling the rapid production of high-quality plastic prototypes and small batch production runs. Its scalability, design flexibility, and cost-effectiveness make it an ideal choice for businesses looking to bring their products to market quickly and efficiently.
Rapid Prototyping
Rapid prototyping is an integral aspect of protofab engineering, enabling the swift creation of physical prototypes from digital designs. It plays a crucial role in product development, allowing engineers and designers to quickly iterate and refine their concepts, leading to faster time-to-market and reduced development costs.
- Accelerated Design Iteration: Rapid prototyping empowers engineers to rapidly produce physical prototypes, enabling them to test and evaluate design concepts in a tangible form. This iterative approach allows for quick identification and resolution of design flaws, leading to improved product quality and performance.
- Enhanced Communication: Physical prototypes facilitate effective communication among engineers, designers, and stakeholders. They provide a common reference point for discussions, enabling clear visualization and understanding of design concepts, reducing the risk of miscommunication and costly errors.
- Functional Testing: Rapid prototypes can be used for functional testing, allowing engineers to assess the performance of their designs under real-world conditions. This testing helps identify potential issues early in the development process, preventing costly mistakes during mass production.
- Reduced Time-to-Market: Rapid prototyping significantly reduces the time required to bring products to market. By enabling quick design iteration and validation, businesses can accelerate their product development cycles, gaining a competitive edge in fast-paced markets.
The integration of rapid prototyping into protofab engineering workflows has transformed the product development process, empowering businesses to innovate, reduce costs, and bring groundbreaking products to market faster. It remains a cornerstone of protofab engineering, driving efficiency and enabling the creation of high-quality products.
Product Development
Product development is the backbone of protofab engineering, playing a pivotal role in the realization of innovative and market-ready products. It involves the transformation of concepts into tangible products, encompassing various stages from ideation to design, prototyping, testing, and refinement.
The connection between product development and protofab engineering is symbiotic. Protofab engineering provides the tools and technologies that accelerate product development, enabling rapid prototyping, design iteration, and functional testing. Conversely, product development drives the demand for advanced protofab engineering solutions to meet the evolving needs of designers and engineers.
Real-life examples illustrate the practical significance of this connection. In the automotive industry, protofab engineering has enabled the rapid development and testing of new vehicle designs, reducing time-to-market and improving overall product quality. In the medical device sector, protofab engineering has facilitated the creation of patient-specific implants and surgical tools, leading to improved patient outcomes and reduced healthcare costs.
Understanding the connection between product development and protofab engineering empowers businesses to enhance their innovation capabilities, reduce development time, and bring superior products to market. It highlights the importance of close collaboration between product development teams and protofab engineering experts to achieve optimal results.
Design Iteration
Design iteration is an inherent and crucial component of protofab engineering, enabling the refinement and improvement of product designs through repeated cycles of testing, analysis, and modification. It plays a pivotal role in ensuring that products meet the desired specifications, perform as intended, and align with market demands.
Protofab engineering provides the tools and technologies that facilitate rapid design iteration. Rapid prototyping techniques, such as 3D printing and CNC machining, allow engineers to quickly create physical prototypes, enabling them to test and evaluate design concepts in a tangible form. This iterative approach reduces the time and cost associated with traditional manufacturing methods, allowing for more frequent and comprehensive design evaluations.
Real-life examples demonstrate the practical significance of design iteration in protofab engineering. In the aerospace industry, design iteration has enabled the development of lightweight and aerodynamic aircraft components, leading to improved fuel efficiency and reduced emissions. In the consumer electronics sector, design iteration has facilitated the creation of sleek and user-friendly devices, enhancing the overall user experience.
Understanding the connection between design iteration and protofab engineering empowers businesses to optimize their product development processes. By leveraging advanced protofab technologies and embracing an iterative design approach, businesses can reduce time-to-market, improve product quality, and gain a competitive edge in their respective markets.
Cost-Effectiveness
Cost-effectiveness is a defining characteristic of protofab engineering, enabling businesses to develop and produce products in a financially viable manner. It encompasses various aspects that contribute to optimizing resource allocation and minimizing production costs.
- Reduced Material Waste: Protofab engineering techniques, such as 3D printing and CNC machining, minimize material waste by utilizing precise cutting and additive manufacturing processes. This reduces raw material costs and promotes sustainable manufacturing practices.
- Rapid Prototyping: Rapid prototyping capabilities allow for quick design iteration and testing, reducing the need for expensive tooling and minimizing the cost of design changes. This iterative approach optimizes the design process, leading to cost savings and improved product quality.
- Small Batch Production: Protofab engineering enables cost-effective production of small batches, catering to niche markets or specific customer requirements. This flexibility reduces the financial burden of large-scale production runs and allows businesses to test market demand before committing to mass production.
- Design for Manufacturability: Protofab engineering promotes design for manufacturability (DFM) principles, ensuring that products are designed with production efficiency in mind. This reduces manufacturing costs, simplifies assembly processes, and minimizes the need for rework or costly modifications.
In conclusion, the cost-effectiveness of protofab engineering stems from its ability to minimize material waste, facilitate rapid prototyping, enable small batch production, and promote design for manufacturability. These aspects collectively contribute to reducing production costs, optimizing resource allocation, and enhancing overall financial viability in product development.
Flexibility
Flexibility is a defining characteristic of protofab engineering, empowering businesses with the agility to adapt to changing market demands, explore innovative designs, and respond efficiently to customer needs. This versatility stems from several key facets:
- Rapid Prototyping: Protofab engineering enables rapid prototyping, allowing engineers to quickly create physical prototypes of their designs. This flexibility facilitates iterative design processes, enables thorough testing, and reduces the time and cost associated with design changes.
- Design Customization: Protofab engineering provides the flexibility to customize designs to meet specific requirements or target niche markets. This customization capability allows businesses to cater to specialized applications, fulfill unique customer needs, and differentiate their products in competitive markets.
- Material Versatility: Protofab engineering utilizes a wide range of materials, including metals, plastics, and composites. This material versatility empowers engineers to select the most appropriate materials for each application, considering factors such as strength, weight, and cost, thus optimizing the performance and value of the final product.
- Small Batch Production: Protofab engineering enables cost-effective production of small batches, allowing businesses to test market demand, refine designs, and respond to changing customer needs without the financial burden of mass production.
In conclusion, the flexibility of protofab engineering lies in its ability to facilitate rapid prototyping, enable design customization, leverage material versatility, and support small batch production. These facets collectively empower businesses to adapt to dynamic market conditions, explore innovative concepts, and deliver tailored products that meet the evolving needs of their customers.
Customization
Customization has emerged as a defining characteristic of protofab engineering, empowering businesses to craft products tailored to specific needs, market niches, and individual customer preferences. This ability to customize designs and cater to unique requirements sets protofab engineering apart from traditional manufacturing approaches.
- Design Flexibility: Protofab engineering enables the creation of highly customized designs, allowing engineers to explore innovative concepts and tailor products to specific applications. This flexibility empowers businesses to differentiate their offerings, cater to specialized markets, and fulfill unique customer demands.
- Rapid Prototyping: Protofab engineering facilitates rapid prototyping, enabling engineers to quickly create physical prototypes of customized designs. This iterative approach allows for thorough testing, design refinement, and validation, ensuring that the final product meets the desired specifications and customer expectations.
- Material Versatility: Protofab engineering utilizes a wide range of materials, including metals, plastics, and composites. This material versatility empowers engineers to select the most appropriate materials for each customized design, considering factors such as strength, weight, and cost, thus optimizing the performance and value of the final product.
- Small Batch Production: Protofab engineering enables cost-effective production of small batches, making it feasible to produce customized products without the financial burden of mass production. This flexibility allows businesses to test market demand, refine designs, and respond to changing customer needs with greater agility.
In conclusion, the connection between customization and protofab engineering is multifaceted, empowering businesses to create tailored products that meet the diverse needs of their customers. Protofab engineering provides the flexibility, rapid prototyping capabilities, material versatility, and cost-effective small batch production capabilities that are essential for successful customization.
Frequently Asked Questions about Protofab Engineering
This section aims to address frequently asked questions about protofab engineering, providing informative answers to common concerns or misconceptions. By understanding these key aspects, individuals can better appreciate the value and applications of protofab engineering.
Question 1: What sets protofab engineering apart from traditional manufacturing methods?
Protofab engineering distinguishes itself through its emphasis on rapid prototyping, design flexibility, and cost-effective production of small batches. This approach empowers businesses to quickly iterate on designs, explore innovative concepts, and cater to specialized market needs.
Question 2: How does protofab engineering contribute to product development?
Protofab engineering plays a crucial role in product development by enabling rapid prototyping and design iteration. By creating physical prototypes quickly and cost-effectively, protofab engineering allows engineers to test and refine their designs, reducing time-to-market and improving product quality.
Question 3: What are the key benefits of using protofab engineering for small batch production?
Protofab engineering offers several advantages for small batch production, including cost-effectiveness, design customization, and material versatility. This approach allows businesses to test market demand, fulfill niche orders, and produce custom products without the high costs associated with mass production.
Question 4: How does protofab engineering promote sustainability in manufacturing?
Protofab engineering contributes to sustainability by minimizing material waste through precise manufacturing techniques. Additionally, by enabling small batch production, protofab engineering reduces the environmental impact associated with overproduction and disposal of excess inventory.
Question 5: What are the limitations or challenges associated with protofab engineering?
While protofab engineering offers many advantages, it also has certain limitations. These include potential constraints on production volume, material selection, and the need for skilled engineers to operate the specialized equipment.
Question 6: How can businesses leverage protofab engineering to gain a competitive edge?
Businesses can harness protofab engineering to gain a competitive edge by rapidly bringing innovative products to market, responding to changing customer demands, and optimizing their manufacturing processes for efficiency and cost-effectiveness.
In conclusion, protofab engineering offers a transformative approach to product development and manufacturing, providing businesses with the agility, flexibility, and cost-effectiveness to succeed in today's dynamic markets.
Learn more about Protofab Engineering
Protofab Engineering Tips
Protofab engineering offers a powerful approach to product development and manufacturing, enabling businesses to innovate more efficiently and cost-effectively. Here are some valuable tips to optimize your use of protofab engineering:
Tip 1: Leverage Rapid Prototyping for Design Iteration:
Rapid prototyping allows for quick and affordable creation of physical prototypes, enabling iterative design refinement. This reduces the time and cost associated with traditional manufacturing methods, leading to improved product quality and faster time-to-market.
Tip 2: Utilize Design for Manufacturability Principles:
Incorporating design for manufacturability principles ensures that your designs are optimized for production efficiency and cost-effectiveness. This involves considering factors such as material selection, part geometry, and assembly processes during the design phase.
Tip 3: Explore Material Versatility:
Protofab engineering provides access to a wide range of materials, including metals, plastics, and composites. Explore different materials to find the optimal balance of strength, weight, and cost for your specific application.
Tip 4: Capitalize on Small Batch Production:
Protofab engineering enables cost-effective production of small batches, allowing you to test market demand, fulfill niche orders, and produce custom products without the high costs associated with mass production.
Tip 5: Collaborate with Experienced Protofab Engineers:
Protofab engineering requires specialized knowledge and expertise. Collaborating with experienced protofab engineers ensures that your projects are executed efficiently and effectively, maximizing the benefits of this transformative technology.
By following these tips, you can harness the full potential of protofab engineering to streamline your product development process, reduce costs, and bring innovative products to market faster.
Learn more about Protofab Engineering
Conclusion
Protofab engineering has emerged as a transformative force in product development and manufacturing, empowering businesses with unprecedented agility, flexibility, and cost-effectiveness. Through advanced technologies such as 3D printing, CNC machining, and injection molding, protofab engineering enables rapid prototyping, design iteration, and small batch production.
This innovative approach has revolutionized the way products are brought to market, reducing time-to-market, improving product quality, and allowing for tailored solutions that meet specific customer needs. As technology continues to advance and protofab engineering becomes more accessible, businesses that embrace this transformative approach will be well-positioned to succeed in the competitive global marketplace.
Youtube Video:
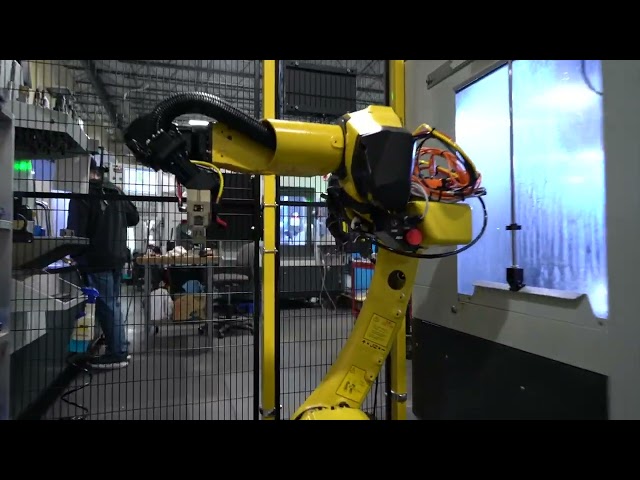